In the packaging industry, as in any industry, it is sometimes necessary to perform tests of the validity of the product options. For packaging, the ideal tests would come from real world situations and many tests do. Of course, that is not always possible, which is why throughout the years, many standard tests have been developed and some have even been refined (which requires testing tests). ASTM International (formerly the American Society for Testing and Materials), ISO, militaries and other organizations keep track of these standard tests and suggest the standard approach for performing them. Many testing companies also add on to these standards or adjust them slightly for their own testing purposes.
We at Liberty Packaging specialize in anti-corrosive and anti-static packaging and are thus most interested in the standard tests for these situations. The tests most commonly used for corrosion testing are temperature/humidity tests, salt spray tests, UV tests, mixed flowing gas tests and cyclic tests. These are discussed below. The most common test for anti-static packaging is the application of a surface resistivity meter. Of course, the packaging must be in the dissipative range (10^5 - 10^11 Ω/meter squared) for true electrostatic discharge protection.
Temperature/humidity tests comprise situations where the temperature and/or humidity are adjusted, usually to higher levels, to create a corrosive environment (or low levels to test ESD properties). These tests will often start with a few hours of increasing temperature followed by a few hours of increasing humidity and then the product will stay in this situation for several days.
Salt spray tests are similar to temperature tests in that they include a higher temperature, but as the name suggests, salt spray (or salt fog) tests add a salt solution that is sprayed throughout the test cabinet. The cabinets are usually specifically designed to provide consistent spraying and the concentration of the solution is based on a standard, e.g. ASTM B117 - 11 Standard Practice for Operating a Salt Spray (Fog) Apparatus.
UV tests simply place an item within a test cabinet that has been fitted to provide ultra violet light in an attempt to facilitate the break down of the packaging material as well as potential degradation on the item. These tests can include changes of temperature and humidity.
Mixed flowing gag tests were developed by a consortium to more realistically create an accelerated scenario for items in different world regions using corrosive gases which are pumped into the test cabinet so as to provide set gas concentrations depending on the region of interest. The gases used are most often hydrogen sulfide, chlorine, and nitrous oxides with the occasional addition of ozone and/or sulfur dioxide depending on the test standard and the company performing it. These gases are the biggest causes of corrosion in the environments throughout the world and can most accurately predict how packaging will perform with time.
Cyclic tests, typically UV, humidity and/or salt spray tests, were developed to try to create a worst-case scenario for packaging. The item can be rotated through various tests, such as the UV chamber and tested for several hours or days and then removed and placed into the salt spray test and then the process is repeated to the desire of the testers, or cycled within one test.
All of these tests are designed to simulate an accelerated corrosion environment. Often testers try to relate the results of the test to practical numbers about how long something will last in the real world, but it can be difficult and it seems there is no real standard for the relationship between these tests and real world situations. The best use is for comparative purposes between two packaging schemes tested at the same time under one of the above protocols.
For more on how corrosion works watch our Corrosion Video
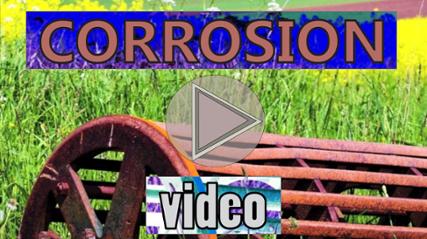
Liberty Intercept Blog
Standard Corrosion Tests
Posted by Elaine Spitz on Dec 8, 2014 1:46:00 PM
We at Liberty Packaging specialize in anti-corrosive and anti-static packaging and are thus most interested in the standard tests for these situations. The tests most commonly used for corrosion testing are temperature/humidity tests, salt spray tests, UV tests, mixed flowing gas tests and cyclic tests. These are discussed below. The most common test for anti-static packaging is the application of a surface resistivity meter. Of course, the packaging must be in the dissipative range (10^5 - 10^11 Ω/meter squared) for true electrostatic discharge protection.
Temperature/humidity tests comprise situations where the temperature and/or humidity are adjusted, usually to higher levels, to create a corrosive environment (or low levels to test ESD properties). These tests will often start with a few hours of increasing temperature followed by a few hours of increasing humidity and then the product will stay in this situation for several days.
Salt spray tests are similar to temperature tests in that they include a higher temperature, but as the name suggests, salt spray (or salt fog) tests add a salt solution that is sprayed throughout the test cabinet. The cabinets are usually specifically designed to provide consistent spraying and the concentration of the solution is based on a standard, e.g. ASTM B117 - 11 Standard Practice for Operating a Salt Spray (Fog) Apparatus.
UV tests simply place an item within a test cabinet that has been fitted to provide ultra violet light in an attempt to facilitate the break down of the packaging material as well as potential degradation on the item. These tests can include changes of temperature and humidity.
Mixed flowing gag tests were developed by a consortium to more realistically create an accelerated scenario for items in different world regions using corrosive gases which are pumped into the test cabinet so as to provide set gas concentrations depending on the region of interest. The gases used are most often hydrogen sulfide, chlorine, and nitrous oxides with the occasional addition of ozone and/or sulfur dioxide depending on the test standard and the company performing it. These gases are the biggest causes of corrosion in the environments throughout the world and can most accurately predict how packaging will perform with time.
Cyclic tests, typically UV, humidity and/or salt spray tests, were developed to try to create a worst-case scenario for packaging. The item can be rotated through various tests, such as the UV chamber and tested for several hours or days and then removed and placed into the salt spray test and then the process is repeated to the desire of the testers, or cycled within one test.
All of these tests are designed to simulate an accelerated corrosion environment. Often testers try to relate the results of the test to practical numbers about how long something will last in the real world, but it can be difficult and it seems there is no real standard for the relationship between these tests and real world situations. The best use is for comparative purposes between two packaging schemes tested at the same time under one of the above protocols.
For more on how corrosion works watch our Corrosion Video
Topics: anti-corrosion, corrosion resistance, manufacturing, anti-corrosion barrier packaging, corrosion prevention, standard tests
Related Posts
Boston's Time Capsule - Contents Preserved with Copper: Part Two
Corrosion on Guitar Strings and How to Solve with Packaging
Leave a Comment