Efficiency is important. Having to do a job two or three times in order to make it right is a waste; it's also not very much fun either (you are currently reading my third draft). There are times where such redundancy is necessary. An example we at the ITG use to display this is the case of the armor-plated Humvee cabs.
The peace dividend, widely heralded back in the mid 90’s, created just sort of a scenario in the case of Humvees. Through design changes (to reduce cost, weight and other factors) there was a series of Humvees built that had a lighter armor plate. This proved to be a costly mistake when they were deployed during the Second Gulf War.
A staple in Middle Eastern conflicts has been the Improvised Explosive Device (IED). The lack of heavy-duty armor plating on the light Humvees made our troops especially susceptible to this type of attack. So they needed to be fixed before any more unnecessary injuries occurred.
The problem was that the Humvees needing retrofitting were already deployed in Kuwait, but the heavy-duty cabins were in Texas. A large problem with delivery of such an item is the amount of open air or dead space there is in and around the irregularly-shaped cabin. Traditional corrosion protection needs to be within a relatively close proximity to metal surfaces to prevent degradation. This would have meant an inefficient pack out, which still may have fallen short due to the complex physical properties of the item and pallet.
What we did was line the crate with Intercept material. Even though our Intercept packaging material was not touching the metal surface, we were able to create a corrosion gas free environment for the new cabs in transit. This allowed the cabins to arrive in pristine condition and ready to be installed immediately. The real ingenuity of this plan was revealed in the return ship. After the Intercept lined crates were emptied, the old cabins were uninstalled and sent back to Texas in the same Intercept-protected crates.
There were many instances of inefficiency in this story, but I am proud to say Intercept helped avoid more while helping to properly protect our soldiers. Even though the first cabins were not ideal for the combat conditions, a lot of resources were invested in their fabrication, making a slow rusty death outside of an Kuwaiti Army base all the more painful. Instead of 2000 of these cabins being laid to waste, we shipped them back in the same crate, also rust and corrosion free, ready to be reused, avoiding more waste.
The cleverness of the packaging strategy saved our country millions of dollars in wasted manufacturing and materials and was recognized by NIPHLE (National Institute of Packaging, Handling, and Logistics Engineers) as an award-winning packaging design. Regardless of accolades, I am proud to be part of a company that came up with a procedure to help our country protect its protectors and avoid costly and wasteful inefficiency.
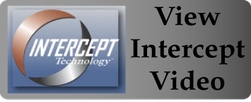
Intercept Technology Packaging products fit within a sustainability strategy because they are reusable, recyclable, do not contain or use volatile components (No VOCs, Not a VCI) and leave a smaller carbon footprint than most traditional protective packaging products.
Liberty Intercept Blog
Packaging Humvees with Award-Winning Intercept
Posted by Elaine Spitz on May 16, 2012 10:25:00 AM
The peace dividend, widely heralded back in the mid 90’s, created just sort of a scenario in the case of Humvees. Through design changes (to reduce cost, weight and other factors) there was a series of Humvees built that had a lighter armor plate. This proved to be a costly mistake when they were deployed during the Second Gulf War.
A staple in Middle Eastern conflicts has been the Improvised Explosive Device (IED). The lack of heavy-duty armor plating on the light Humvees made our troops especially susceptible to this type of attack. So they needed to be fixed before any more unnecessary injuries occurred.
The problem was that the Humvees needing retrofitting were already deployed in Kuwait, but the heavy-duty cabins were in Texas. A large problem with delivery of such an item is the amount of open air or dead space there is in and around the irregularly-shaped cabin. Traditional corrosion protection needs to be within a relatively close proximity to metal surfaces to prevent degradation. This would have meant an inefficient pack out, which still may have fallen short due to the complex physical properties of the item and pallet.
What we did was line the crate with Intercept material. Even though our Intercept packaging material was not touching the metal surface, we were able to create a corrosion gas free environment for the new cabs in transit. This allowed the cabins to arrive in pristine condition and ready to be installed immediately. The real ingenuity of this plan was revealed in the return ship. After the Intercept lined crates were emptied, the old cabins were uninstalled and sent back to Texas in the same Intercept-protected crates.
There were many instances of inefficiency in this story, but I am proud to say Intercept helped avoid more while helping to properly protect our soldiers. Even though the first cabins were not ideal for the combat conditions, a lot of resources were invested in their fabrication, making a slow rusty death outside of an Kuwaiti Army base all the more painful. Instead of 2000 of these cabins being laid to waste, we shipped them back in the same crate, also rust and corrosion free, ready to be reused, avoiding more waste.
The cleverness of the packaging strategy saved our country millions of dollars in wasted manufacturing and materials and was recognized by NIPHLE (National Institute of Packaging, Handling, and Logistics Engineers) as an award-winning packaging design. Regardless of accolades, I am proud to be part of a company that came up with a procedure to help our country protect its protectors and avoid costly and wasteful inefficiency.
Intercept Technology Packaging products fit within a sustainability strategy because they are reusable, recyclable, do not contain or use volatile components (No VOCs, Not a VCI) and leave a smaller carbon footprint than most traditional protective packaging products.
Topics: waste, corrosion resistance, how to reduce waste, outdoor storage
Related Posts
For Optimal Efficiency - Automobiles and Packaging
Intercept Packaging - Joe's Creative Uses at Home - Paint Cans
Packaging the Husky - Household Applications Series
Leave a Comment