While cleaning out the office this holiday season, we came across our very first newsletter sent by U.S. Mail to our contacts in 1996. Since the inception of Liberty Packaging, our basic marketing philosophy has been to share information about Intercept Technology™ packaging materials. Seventeen years later, it occurs to me that the information shared remains as valuable now to any company manufacturing electronics; devices, boards, and assembling full units. Intercept Technology barrier packaging was disruptive technology compared to the rest of the barrier products in use at that time.
The 1996 newsletter entitled: “AT&T - Rust Was the Problem” discussed how AT&T determined a major cause of defects to their circuits and circuit cards had been corrosion.
- Corrosion can inhibit solid solder joints
- Corrosion can cause a narrowing for electrical paths, causing more susceptibility to heat buildup and burnouts.
- Corrosion buildup has been proven to increase the intensity of electrostatic discharge events.
- Corrosion, limiting electron flow, can strain power supplies.
For those reasons, the afore-mentioned newsletter stated analysis from AT&T manufacturing that when their circuit cards were protected from corrosion by Static Intercept®, they were able to ship six and a half million boards without a defect. That is an amazing testament to the effects of Intercept Technology packaging.
The basic concept still makes sense. Atmospheric gases that cause corrosion need to neutralize and metals need to react with them. Nature is always seeking balance. Unfortunately, that process isn’t necessarily a good thing when building products like electronics. An easy solution for AT&T was to wrap their electronics in Static Intercept bags, similar to putting a heavy duty “skin” around their product. The Intercept Technology packaging solution makes just as much sense, perhaps even more so, today.
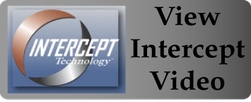
Intercept Technology Packaging products fit within a sustainability strategy because they are reusable, recyclable, do not contain or use volatile components (No VOCs, Not a VCI) and leave a smaller carbon footprint than most traditional protective packaging products.
Liberty Intercept Blog
Best Packaging for Electronics: Then and Now
Posted by Joe Spitz on Jan 8, 2013 10:13:00 PM
The 1996 newsletter entitled: “AT&T - Rust Was the Problem” discussed how AT&T determined a major cause of defects to their circuits and circuit cards had been corrosion.
For those reasons, the afore-mentioned newsletter stated analysis from AT&T manufacturing that when their circuit cards were protected from corrosion by Static Intercept®, they were able to ship six and a half million boards without a defect. That is an amazing testament to the effects of Intercept Technology packaging.
The basic concept still makes sense. Atmospheric gases that cause corrosion need to neutralize and metals need to react with them. Nature is always seeking balance. Unfortunately, that process isn’t necessarily a good thing when building products like electronics. An easy solution for AT&T was to wrap their electronics in Static Intercept bags, similar to putting a heavy duty “skin” around their product. The Intercept Technology packaging solution makes just as much sense, perhaps even more so, today.
Intercept Technology Packaging products fit within a sustainability strategy because they are reusable, recyclable, do not contain or use volatile components (No VOCs, Not a VCI) and leave a smaller carbon footprint than most traditional protective packaging products.
Topics: American manufacturing, heavy duty barrier packaging, Static Intercept
Related Posts
Contamination Testing
Packaging's Crucial Role vs FOD
Customer Service with a Smile
Leave a Comment